Reducing the risks of exposure to hazardous substances
On building sites, in laboratories, in industrial spaces, as well as in hairdressing salons or when cleaning: people come into contact with chemical agents in many workplaces. As an employer, you can protect the health of those employees by carrying out a hazardous substance risk assessment. It shows in which situations it is best to carry out exposure measurements. Prevention advisor Fabian Bosson explains the when, how, and why of these measurements.
When do you need to take a measurement?
To assess whether your employees are at real risk from exposure to hazardous substances, you should first carry out a so-called basic characterisation. Three questions arise:
- What substances are used and what are the exposure limits? A list of these limit values can be found in the Well-being at Work Codex.
- Which workplace factors influence exposure? Consider frequency and duration of the work safety procedures, temperature, pressure, (personal and collective) protective equipment, etc.
- What is the exposure? This estimate is made on the basis of previous measurements, directly readable measuring equipment, measurement results of similar installations or work processes, data from literature or exposure models, etc.

Example
You have a painting business. What kind of paint do your employees use and what harmful substances does it contain? Do your employees work in a ventilated environment and use a mask and/or gloves? Do you have data to estimate the extent to which your workers are exposed to the substances?
You use this information to determine whether measurements are necessary. There are three possibilities:
- No risk of exposure: the estimated exposure is far below the limit value. You don’t have to take any measurements; just keep monitoring the situation.
- Exposure hazard: Take the necessary measures to reduce exposure. Then have measurements carried out for verification.
- No conclusion: measurements are needed to assess whether the situation is safe.
How does a measurement process work?
Please contact an occupational hygiene prevention advisor for exposure measurements. This person first divides your employees into homogeneous job groups. These are groups of people who do roughly the same job and are therefore exposed to similar risks.
Example
Do five workers in the same room perform tasks with approximately the same exposure? Then a measurement by some of them may be sufficient for representative results.
The prevention advisor draws up a measurement plan using this information. This plan includes several measurements per homogeneous job group, as one measurement is not enough to be sure that there is no risk of exposure.
During the measurements, your prevention advisor follows the requirements of standard NBN-EN 689 for measuring chemical substances. The measurements are taken in the breathing zone of your employees during their work (personal air sampling). This is more reliable than stationary space measurements.
After the measurements, the occupational hygiene prevention advisor draws up a measurement report with all the results. If this reveals that your employees are at risk of exposure, the advisor will discuss the possible causes with you and give you recommendations for reducing exposure.
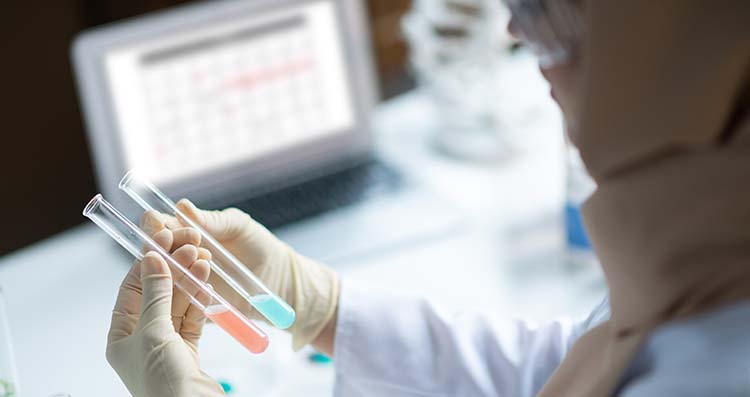
Why do you have to keep taking new measurements?
New measurements need to be taken regularly to ensure the continued safety of your employees. After all, various factors can influence the exposure risks over time. These include changes in work processes, wear and tear of work equipment or installations, and reduced technical performance of the ventilation system. The NBN-EN 689 standard determines whether you must perform a new measurement after 12, 18, 24, or 36 months.
Measurements are absolutely necessary to assess the exposure to chemical substances objectively. After all, employees quickly become accustomed to a chemical substance – just think of the smell of paint. Often, they don’t experience any physical discomfort during their work, but there are dangerous long-term effects. For example, high exposure to quartz dust is very carcinogenic.
In addition to exposure measurements, protective equipment is an important part of the solution. We are talking about both collective (e.g. a ventilation system) and personal (e.g. gloves or a mask) equipment.
How can Mensura help you?
Download our infographic: Quartz dust: here's what you need to know.
Need help carrying out a measurement? Our environmental experts are happy to assist you! Leave your details in the form below and we will contact you as soon as possible.