What is the difference between an inspection and assessment of work and protective equipment?
An inspection or assessment of your employees’ work and protective equipment helps you guarantee their safety. But did you know that an inspection and assessment are not the same thing? These are the differences – and the consequences.
Inspections: clear rules
An inspection is an obligation that is clearly described in the Codex, Belgian General Labour Protection Rules (ARAB) or Belgian General Regulations for Electrical Installations (AREI). Only EDTCs (external services for technical inspections in the workplace) may carry out these inspections and provide a written report afterwards.
Who can you contact regarding an inspection of your work equipment?
The following information is available for each type of inspection:
- How often the inspection needs to be repeated. After every inspection, you will receive a report stating the deadline by which the next inspection must be carried out. The results and any action points will also be included. You are required to save the report for the last inspection conducted.
- Or it involves an inspection before commissioning. If so, you will need to save the report for the entire service life of the approved installation.
Are you purchasing new work equipment? Then it is best to mention in the safety requirements that you also want to receive a conforming inspection report of the work equipment upon delivery.
You are required to contact an EDTC to request the first technical inspection of work equipment that is already in use. Afterwards, the external service will take the initiative to schedule a new inspection. Is the EDTC unable to carry out the inspection by the deadline? The service is required to inform the employer of this no later than ten days before the deadline.
Tip: Keep track of the final deadline of the inspection report for all work equipment and contact an EDTC early in order to schedule an appointment if necessary. This way, you can be sure that you always have a valid inspection report.
Good to know: for the inspection of pressure vessels and similar equipment, you do not contact an EDTC, but an authorised environmental expert.
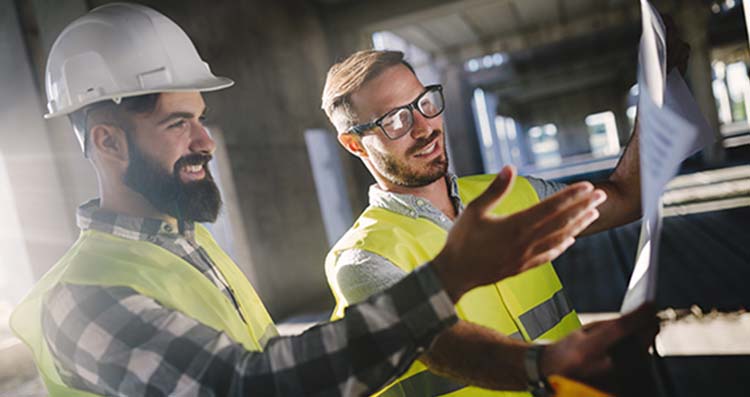
Assessment: less strict requirements
The most important goal of an assessment is to determine whether the work or protective equipment is still in proper condition. Consider, for example, an assessment of the fire extinguishers. This is mandatory annually, but does not necessarily need to be carried out by an EDTC. An internal employee with expertise or a specialised company can also do this.
These are the most important differences between an assessment and an inspection:
- Code of good practice: Organisations must have work and protective equipment assessed at least annually. That frequency can be increased if the risk analysis shows it is necessary.
- An assessment report is not always provided. A clear inspection report is always provided after an inspection, while the ‘proof’ of an assessment is usually no more than a sticker or coloured strap. Importantly, you should be able to demonstrate an assessment when a serious occupational accident occurs. Don’t have proof of an assessment? Then you are no longer legally compliant.
An assessment is carried out by a ‘qualified professional’. These professionals are expected to have demonstrable expertise. Thus, the necessary training and experience are essential. For example, training is mandatory to assess scaffolding.
The list of assessors is longer than the EDTCs for inspections. Think of your in-house prevention adviser. They may be a qualified professional or another person designated to carry out internal assessments. But external assessments are also often a good solution. In that case, you can turn to EDTCs or specialised firms, which have the necessary certificates. For example, does your organisation have a sprinkler system? Then you should only have it assessed by an approved company.
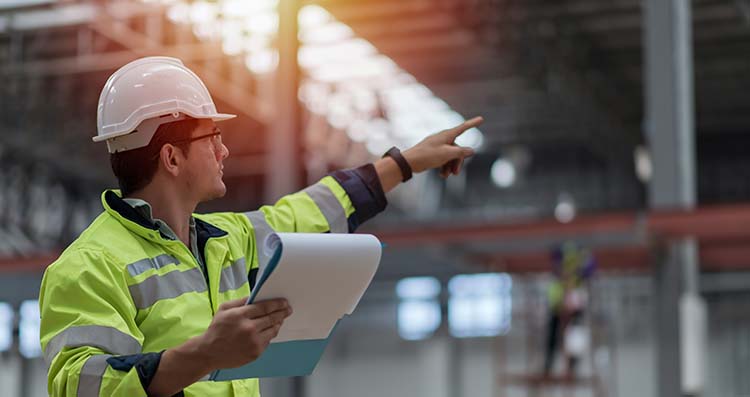
Forklift truck: inspection or assessment?
There is quite a bit of confusion regarding the periodic assessment of forklift trucks. Many people believe that an inspection is always required, but an assessment by a qualified professional is sufficient with ‘normal use’.
However, a forklift truck requires an inspection if it carries a load (making it a hoisting device) or is used to elevate people using a personnel basket (making it an aerial platform). In these cases, you need to use an EDTC prior to commissioning and periodic inspection, but your forklift also requires a regular assessment.
Similar legal risks
If work or protective equipment is not in proper order according to the inspection or assessment requirements, as an employer, you run the risk of serious legal consequences if a violation or – worse still – an accident occurs that results in physical injury or property damage. After all, you are responsible for the well-being of your employees at all times.
However, this does not alter the fact that your employees also have personal responsibility. Many inspections and assessments take place only a few times a year or even less frequently. So, ask your employees to always check whether work or protective equipment is in proper order before using it. This is often a guidelines or obligation for your employees that is stated in a manual or during training.
Do you have any pressing questions about the inspection or assessment or work and protective equipment?
Contact a Mensura expert using the form below.