Jtekt
JTEKT and Mensura: “field ergonomics”
At the site of Strépy-Bracquegnies, JTEKT Torsen Europe, a branch of Japanese automotive supplier JTEKT, produces limited slip differentials used by many car manufacturers. On one of the assembly lines, workers often pointed out small ergonomic issues. JTEKT asked Mensura for help with this, with a requirement to maintain the line productivity level.
Challenges
- provide workers with an ergonomically excellent work environment
- maintain the assembly line’s productivity
Solutions
- targeted retrofits to reduce physical stess (carried out)
- awareness and training in ergonomic gestures and postures (carried out)
- complete reconfiguration of the line input station (in progress)
Advantages
- decrease in physical stress from work
- workers involved in the improvement process
- strengthening of transparent and constructive communication
- improvement of well-being at work
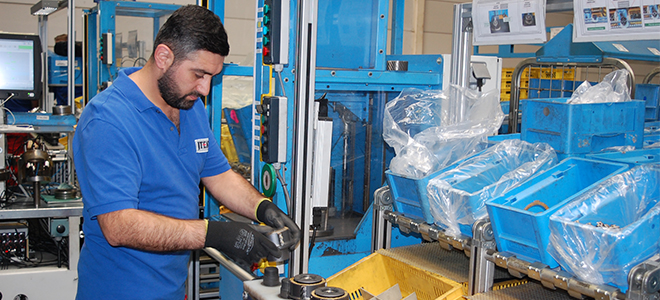
We are open to any changes as long as the workers agree to them. Mensura’s participatory approach has resulted in relevant solutions that are accepted by all."Christelle Delpierre Prevention advisor - Jtekt
At the beginning of 2017, JTEKT turned to Mensura, its long-standing partner in health risk prevention and management, to see how the two workstations on an older generation assembly line could be made more ergonomic.
“Operators regularly complained of minor inconvenience,” says Christelle Delpierre, prevention advisor and maintenance manager at JTEKT: “Racks too far apart, parts difficult to handle... We had already made some changes but we did not know how to go further in our efforts.”
Three stages to improve well-being
In March 2017, the ergonomist assigned by Mensura carried out a first round, observing and gathering information from the operators and the hierarchical line. Her analysis formally identified the ailments reported by workers, and revealed further potential sources of musculoskeletal disorders (MSDs).
“At JTEKT, well-being is more than just a word,” notes ergonomist Caroline Pirotte. “The company is very careful to design workstations ergonomically from the outset, and to give workers regular breaks – ten minutes every hour: I have never seen anything like it. Nevertheless, on this old-fashioned assembly line, the posturerelated stresses were real.”
The next stage started at the end of March. The ergonomist set up two working groups composed of workers from the line’s two workstations, to discuss more in detail and complete her observations. And in April, she presented her recommendations in a multidisciplinary meeting involving both the hierarchical line, process experts and maintenance managers.
“This approach developed at Mensura makes it possible to quickly suggest solutions and then allow them to mature, not just through the exchanges within the company, but also with my fellow ergonomists,” stresses Caroline Pirotte.
A participatory approach
JTEKT requested that a fourth stage be added to the Mensura process: a presentation of the results to all 20 line workers, coubled with training in the ergonomics of handling parts. The prevention advisor explains the rationale behind the request: “We wanted to give operators the opportunity to understand the proposed solutions, and to improve them. But also to realise that it is not just about having an ergonomically designed workstation: some gestures or postures can also be harmful. Mensura was able to answer this request with great flexibility.”
“Mensura implements a participatory approach, and that’s also our philosophy. We encourage communication between operators and the hierarchical line – for example, they share the same workspace. Mensura’s approach has helped to strengthen this communication, which in turn benefits safety and well-being at work.”
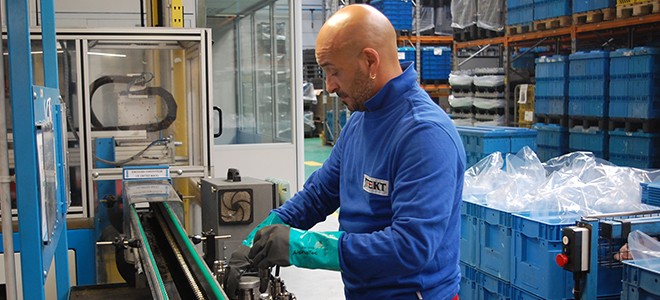
Quick wins and long-term changes
The training sessions-presentations were completed in early 2018. And the easiest changes to implement have now been made. The assembly area is now height adjustable; at the operators’ request, position marks have been added to allow each worker to quickly find the settings that suit him or her. The oil-resistant gloves, which used to make the handling of differentials more difficult, were replaced by a new grip model. Display screens were lowered to eye level. These are but a few examples among many more.
The elements requiring a new design, such as reshaping in an L configuration the current U-shaped line input station, are currently being planned.
Guaranteed production targets
“We are in a factory: we have production targets. We wanted to improve our operators’ well-being at work without jeopardizing our production output. The Mensura approach was 100% in line with our specifications. We implemented field ergonomics, tangible changes, improvements that are achievable and consistent with our production requirements. We are still achieving our goals, and our workers feel better at the end of their day. For us, this is real progress.”
What Mensura can do for you
Mensura helps you face ergonomic challenges through training, ergonomic risk analysis and advice tailored to your organisation.
Need help? Call us on +32 2 549 71 00.