De Kringwinkel Antwerpen
- Home
- What our clients say
- De Kringwinkel Antwerpen
M-pact: more efficient and healthier working conditions at De Kringwinkel Antwerpen
De Kringwinkel Antwerpen automated its household goods sorting department. Fred and Steven, the project initiators, asked for Mensura’s advice on ergonomics. The other Kringwinkel employees were also closely involved.
In our M-pact series, we gauge the positive impact of a project on all parties involved: from managers and project leaders to people in the workplace. We sit together at the table to discuss the collaboration and its outcome.
The project
Over time, the sorting department for household goods of De Kringwinkel Antwerpen had been bursting at the seams. Even though space in the warehouse was limited, the staff had to process more and more items. A redesign – i.e. automation – became necessary, while focusing on the ergonomic aspect. Since the average age of employees in the household goods department is almost 50 years, absenteeism due to physical injuries is a risk. And that’s where Mensura came into the picture.
The protagonists
- Ruth Costers, prevention advisor on ergonomics at Mensura
- Kenny Sebregts, employee in household goods at De Kringwinkel Antwerpen
- Fred Goossens, project manager at De Kringwinkel Antwerpen
- Walter Van den Eynde, head of household goods at De Kringwinkel Antwerpen
- Steven Bosmans, Lean professional at De Kringwinkel Antwerpen
Ruth: “During an intake interview, we exposed the bottlenecks at each work station. By ‘We’ I mean Fred, Steven and I, but also several individuals who are doing those jobs every day. Ultimately, they would be the ones having to work with the new installation. We then converted the outcome of those consultations into designs, which we then discussed with various developers to reduce our selection down to one.”
“My tip for a successful project? From the outset, listen to everyone involved. Including – and especially – your employees. After all, they will be most impacted. Besides, they know best what can be improved in the workplace to achieve optimal results. In this case: more efficient work and less absenteeism.”
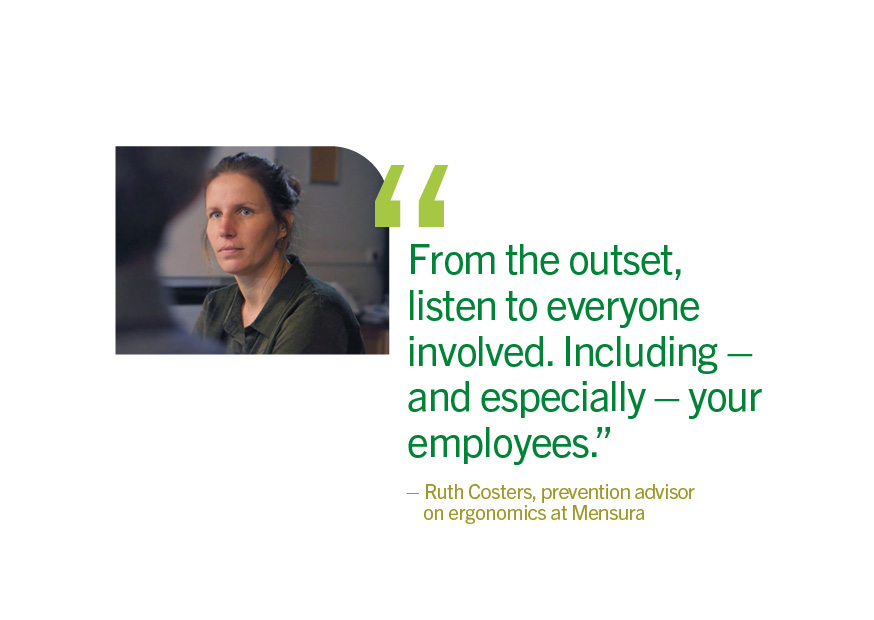
Kenny: “The new system greatly simplifies my work. Without any physical effort, I place the sorted item on the conveyor belt and it automatically ends up with the right people for distribution to the stores. I seem to work faster and with greater efficiency and the task is much less physically demanding. That makes my job a lot easier.”
“Realising that your employer cares about your health and safety is a very nice feeling. I’ve noticed that my colleagues are also happy with the new way of working. And I am actually proud to be able to work with this new, high-tech installation. It’s really worth it.”
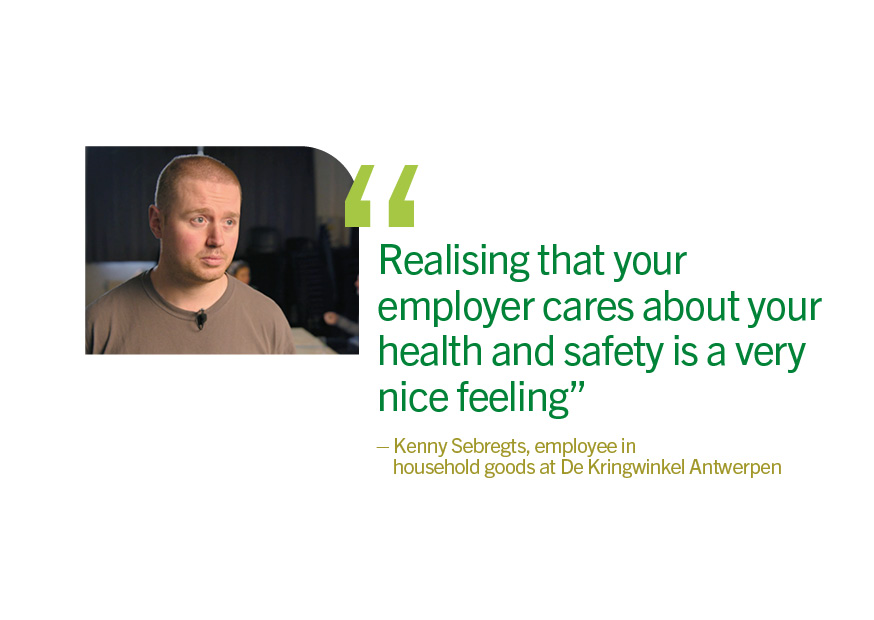
Steven: “Since such an automated process is a premiere in our sector, we could not find any inspiration anywhere. We started from the basic ergonomic principles that Ruth shared with us and then applied them to our household goods department, for each work station. There are more than 40 in total. We regularly created test set-ups and closely involved the supplier of the new installation in the project.”
“At first, there was some concern among our employees. This is understandable since a big change was afoot. But that feeling quickly vanished once they became involved and were allowed to help find solutions. This also helped them understand the usefulness of the redesign. I am convinced that physical health has a major impact on mental well-being. The ergonomic redesign ensures that our employees feel happier in the workplace.”
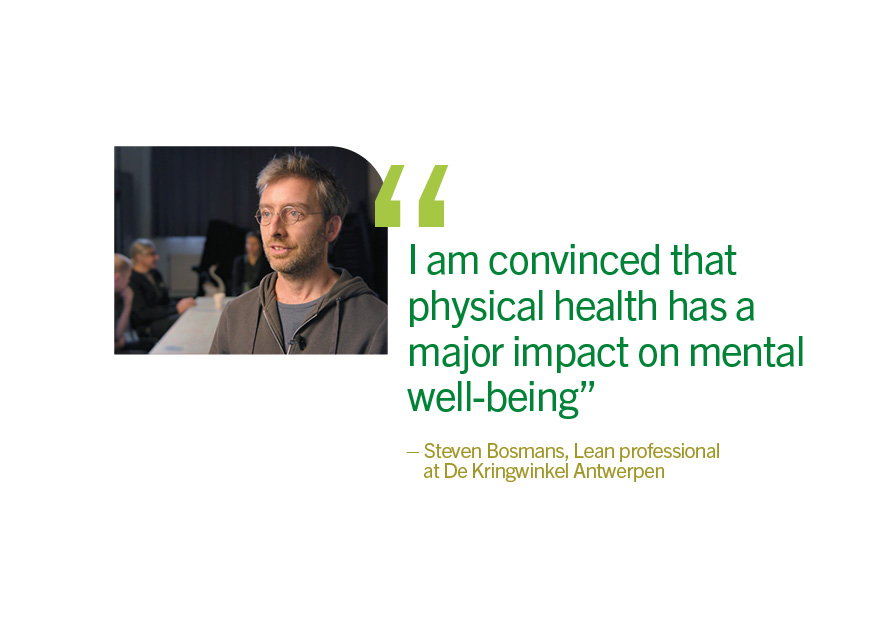
Walter: “Taking the time to listen carefully to the people actually doing the work is crucial in a change process. If the employees see that their input also influences the outcome, then there is a good chance that they will embrace the process. And that is crucial for the impact of the change.”
“Impact can be assessed in two ways. On the one hand, we have hard numbers: the new installation allows us to process more items. Productivity has therefore increased. On the other hand, we have the human aspect: how the employees experience the change and its impact on their physical and mental well-being. In any case, I can see that Kenny is happy at work. For me, this undoubtedly proves that the new installation is doing its job.”
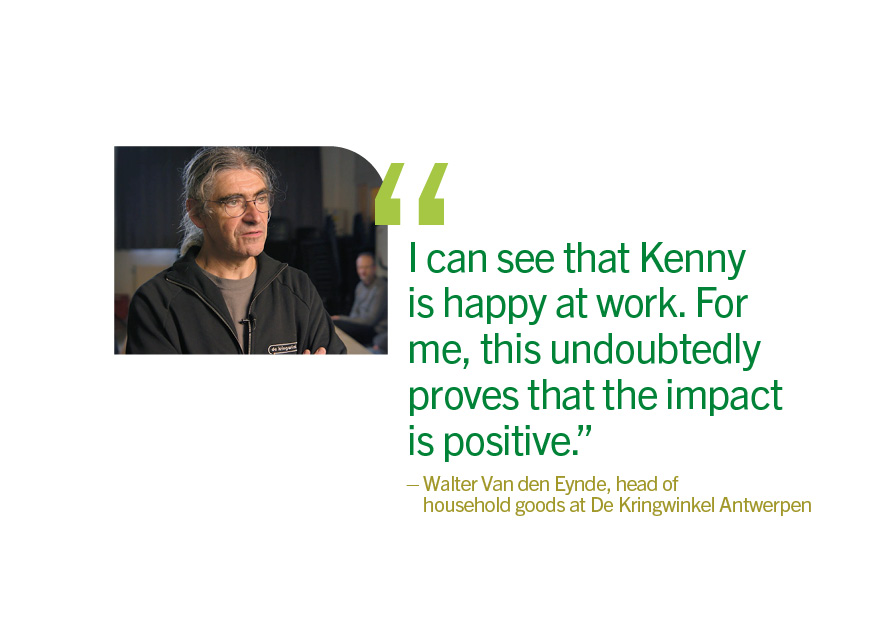
Fred: “The impact of better working conditions for our employees is clearly noticeable. I believe that ergonomics is not just about health, but also about job satisfaction. Investing in people ultimately leads to an increase in productivity as well.”
“The past months have been incredibly exciting. While we learnt a lot from our collaboration with Mensura with regard to ergonomics, it was mainly the interaction with the people doing the work that made the whole project so interesting. We still have many other departments that could use a similar redesign. My ambition is to improve the health of our employees there, too. With higher efficiency as a result.”
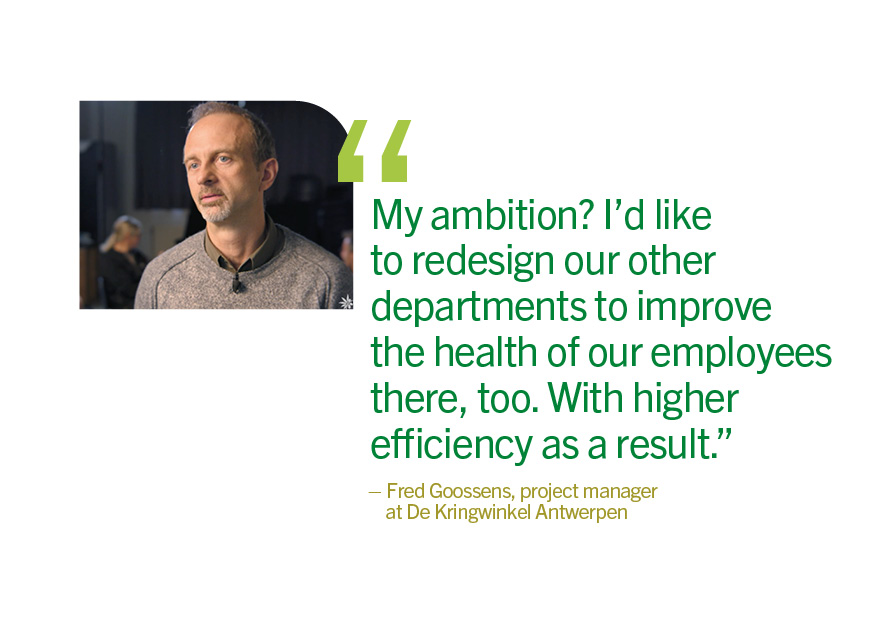
Looking for impactful advice on ergonomics?
E-mail us at ergonomie@mensura.be or call us on +32 2 549 71 00.